I felt frustrated when complex hardware slowed my factory setup, so I searched for a simpler method and found rivet shelving.
Rivet shelving uses interlocking rivets that fit into keyhole slots. This system speeds assembly, reduces snag points, and provides strong storage with minimal tools.
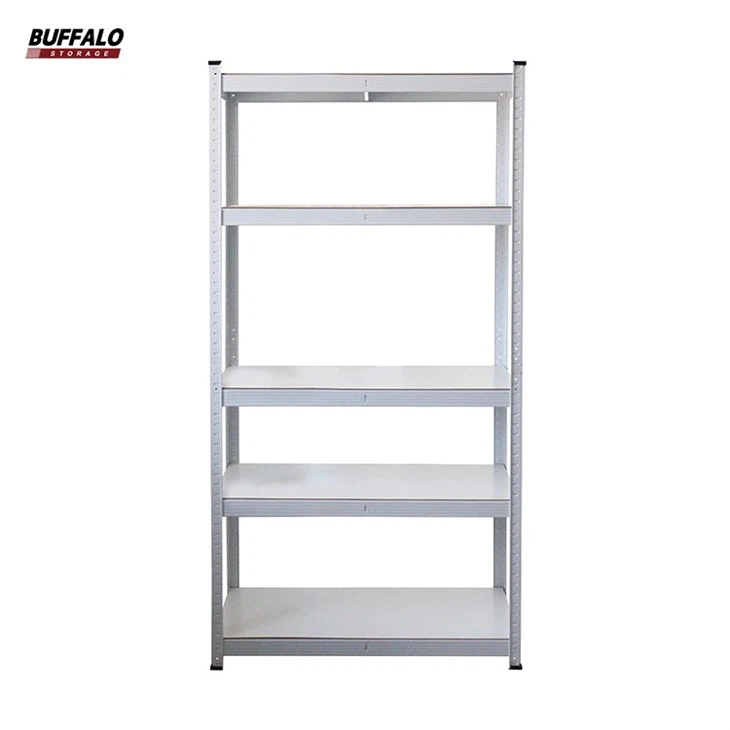
Garage Storage Shelving
My curiosity led me to test rivet systems in many real-world settings. I learned how each rivet locks in place and carries heavy items without extra bolts or complicated parts. I noticed the design is direct, which means teams can assemble racks in minutes. This post covers the main features of rivet shelving, including strength and the advantages of using rivets. I also share my own experiences and insights from Buffalo, where we create shelving solutions for industrial clients who need robust racks without all the stress of traditional hardware.
Is A rivet stronger than a bolt?
I once worked on a factory line that used bolts everywhere, and I wanted to see if rivets could outperform them.
A rivet can match or sometimes exceed a bolt’s strength, depending on the material and load direction. Rivets also resist loosening under vibration.
![]() |
I show a comparison of rivet heads and bolt heads, highlighting their different load paths. |
---|
I want to look at the science behind rivets and bolts to see why one might hold more force than the other. First, a rivet is a permanent fastener that uses a cylindrical body and a head on one side. When we install a rivet, we deform the other side to create a second head that clamps materials together. This means the rivet has no threads to loosen. It also means the body of the rivet can fill the hole more completely than a threaded bolt, which often has a bit of clearance around its shaft. That tight fit translates into uniform load distribution across the rivet’s diameter.
Bolts, on the other hand, rely on tension in the threads and a nut to hold materials together. Vibration and repetitive stress can cause a bolt to work loose if the nut is not secured properly. Many manufacturers add washers or locking mechanisms, but those add complexity. A rivet does not have that risk. The rivet becomes one piece of metal that holds two materials together. It is especially effective in places where vibrations happen, or where a tight seal is needed to prevent small gaps. I once saw an assembly line that used rivets to attach conveyor track sections, and that decision saved them from daily bolt checks. They reported fewer stoppages because rivets stayed tight.
Rivet strength also depends on the rivet’s material. Aluminum rivets bend easily and suit lightweight applications. Steel or stainless steel rivets handle higher loads. The joint design, hole diameter, and metal thickness matter too. In many tests, a properly chosen rivet has shear strength equal or higher than a bolt of similar size. Rivets spread load across a continuous cylinder. A bolt’s threads can introduce stress risers that concentrate force in smaller areas.
I also compare the ease of inspection. A rivet can show signs of shear or stretching if overloaded, which is visible during routine checks. A bolt could be snug, but the threads might be close to stripping, which is less obvious until it fails. In my own work, I encourage clients to pick rivets for racks that stay in one position for years. If they need frequent disassembly, a bolt might be simpler to remove. So, is a rivet stronger than a bolt? It often matches or surpasses a bolt in shear scenarios. It has an edge in vibration resistance and uniform load distribution. That is why many shelving systems use rivets instead of bolts, especially in tough industrial environments where reliability matters more than quick removal.
What is the advantage of rivet?
I remember struggling with loose fasteners in a busy warehouse, which made me wonder if rivets offered a more secure grip.
Rivets do not loosen with vibration, require fewer tools to install, and form a permanent bond that can handle shear loads effectively.
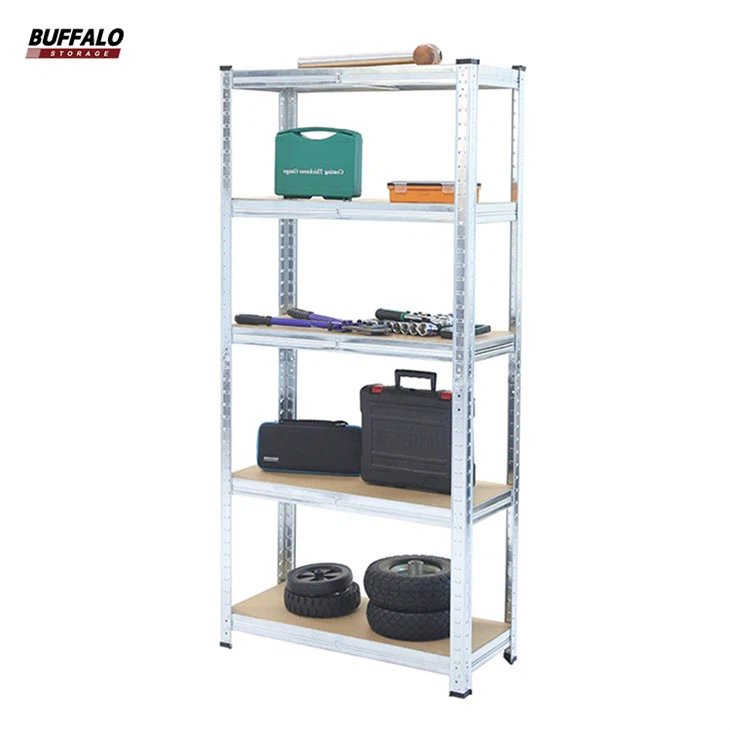
rivet shelving
I want to look closer at how rivets provide an advantage in daily operations. One key benefit is speed of assembly. Workers can place rivets using a rivet gun or specialized press, which forms the second head and locks parts together at once. The process has fewer steps than installing bolts, which need washers, nuts, and consistent torque. By cutting assembly time, workers complete projects faster. In large-scale applications, that can save days of labor and reduce downtime across a production line.
Another big advantage is reliability under shifting loads. I have worked in environments where racks handle heavy boxes one day, then hold small parts the next. If loads swing wildly, rivets tend to hold their tightness. They have no threads that can strip or loosen. This is crucial for warehouses that store goods of different weights on the same level throughout the year. When operators remove or add pallets, the jolts and minor collisions will not shake rivets loose. This durability is essential for safety as well. I have seen forklift drivers accidentally bump into racking legs, and riveted connections did not break or shift. That leads to fewer repairs, fewer hazards, and a more stable inventory system.
A third advantage is the way rivets distribute force. When rivets fill the holes, they spread shear loads evenly across the shank of the rivet. That uniform stress distribution1 reduces the chance of localized failure. In a bolt, the threads can act as weak points because the shape creates stress concentrations. If you need a system that remains static for years, rivets often outlast bolted connections. Some might worry about removing rivets later, but in shelving units designed for permanent or semi-permanent use, that is not a drawback. If I plan to relocate entire shelving units, I can still detach beams from uprights by tapping out rivets or by using a design that uses rivets at the beam ends but still allows reconfiguration of shelf levels.
Finally, I see rivets as a neat solution from a design standpoint. With no exposed nuts or threads, the shelving has fewer snag points for materials, cords, or people’s clothing. This leads to a cleaner look and improved safety in busy aisles. My experience also shows that when people choose riveted racks, they benefit from easier cleaning. Dust and debris do not get stuck in bolt heads. Workers can wipe down surfaces faster. When we talk about advantages, we see that rivets deliver cost savings in assembly, stability in operation, and a streamlined shape that helps with maintenance. These reasons explain why many industrial shelving systems, including Buffalo’s own rivet shelving lines, rely on rivet technology2 for long-term performance.
![]() |
I see a rivet being installed quickly, locking two steel panels together without extra hardware. |
---|
Conclusion
Rivet shelving reduces hassle, speeds installation, and stays strong in tough environments. These simple connections help me build reliable racks with fewer worries day after day.